When laying underground drainage, rigid pipes such as concrete, cast iron and clay have been the material of choice, helping to build a network that has previously been seen as strong enough to withstand the pressures placed upon an underground drainage system. But the use of rigid pipes might be contributing to failure rates and leaks.
In fact, recent research has revealed that plastic pipes offer more flexibility and durability than their rigid cousins, without sacrificing the strength needed to resist the significant pressures that lead to pipe failure.
The dangers of ground movement
Although most people might think ground movement is limited to earthquakes, shifting beneath our feet is more common than many people assume. Ground movement can put pressure on underground pipes and lead to failure and leaks.
The different types of ground movement can be summarised as follows:
- natural settlement - even without an external stimulus such as construction or flooding, the ground shifts and settles over time
- neighbouring excavation or construction - this can change the dynamics of the ground around the site and cause movement
- road traffic - the ebb and flow of traffic contributes to varying pressure on pipework beneath
- shrinking or expanding ground - caused either by flooding, drought, freezing, or by leaking pipes
In fact, the latter poses perhaps the greatest risk to underground pipes as the movement often goes unseen. It’s estimated that 5% of UK mains water supply has been laid in soil with shrink/swell characteristics, and clay soil, for instance, can expand by up to 10% of its original volume, placing significant pressure onto underground pipes.
As such, pipes have historically been built for strength and rigidity in an effort to withstand these pressures. But there are three reasons why strength alone means that rigid pipes are being superseded by flexible alternatives.
The failures of rigid pipes
1. Increasing pressure
In addition to identifying ground movement as a leading cause of tensile failure in cast iron water mains, a report from The European Plastic Pipes and Fittings Association (TEPPFA) also raised deep concerns over rising levels of traffic. It found that increased use of smaller roads intended for only light traffic, as well as new roads being laid over fresh ground, meant that more and more underground pipework was being subjected to pressure it hadn’t been expected to bear when it was originally laid.
The same can be said for some of the leading causes of ground movement. Flooding, drought, and freezing is set to increase with climate change; the unseasonal ‘Beast from the East’ resulted in an almost 200% increase in claims for burst water pipes.
As a result, the pressures being placed on rigid underground pipes are becoming more frequent and more intense. And no matter how strong the pipes have been made, that strength can be undermined by the very forces they’re trying to resist.
2. Corrosion

The UK mains water is supplied predominantly via cast iron pipes, which means it suffers from a further weakness: corrosion. Even if the pipework has been made strong to resist growing tensile pressure, corrosion will weaken its structural strength and leave it vulnerable to failure. In fact, 30% of mains water failures are due to corrosion of cast iron pipes.
These failures can result in more corrosion, resulting in a vicious cycle of leaks, corrosion, and further leaks, culminating in the UK’s mains water supply leaking an incredible 3.17 billion litres of water into the ground every day. And, of course, leaking water pipes can lead to further ground movement which, in turn, affects concrete and clay pipes too.
3. Inflexibility
These growing pressures aren’t a problem if the pipes can withstand them. But the greatest weakness of rigid pipes is their very rigidity. This might seem counter-intuitive at first, but the fact that rigid pipes don’t deform under pressure means these pipes have a literal breaking point; once they are subjected to too much pressure, they fail and they leak.
By contrast, a pipe that was flexible enough to deform under pressure can better handle increasing, regular pressures. Plastic pipes, which are by nature flexible, are also resistant to corrosion, making them less likely to fail. But flexibility and resistance to corrosion aren’t enough; pipes still need to be strong to resist pressure in the first place, which is why the ULTRA3 range of underground drainage is so popular.
The benefits of flexible, plastic pipes
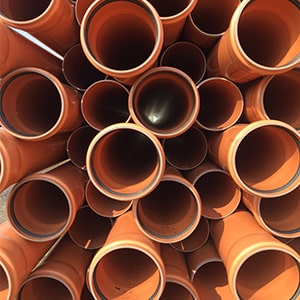
Strength - plastic pipes such as ULTRA3 remain strong by incorporating strengthening features; ULTRA3 features an inner ring of recycled plastics that provide a strong inner core that can resist pressure.
Flexibility - even with this inner core, ULTRA3 can deform under pressure without failing, boasting a superior ability to sustain tensile pressure.
Higher durability - plastic pipes have a greater resistance to corrosion, and have lower defect rates than rigid pipes.
Speed - plastic pipes have a greater resistance to corrosion, and have lower defect rates than rigid pipes.
Sustainable - ULTRA3 pipes, being manufactured from a minimum of 40% recycled material, are also much more sustainable than rigid pipes.
Safer - being lighter than rigid pipes, plastic pipes are easier to handle and work with on-site, reducing risks of accidents.
Longevity - PVCu pipework, like ULTRA3, has been found to have a similar lifespan to traditional materials (such as concrete, cast iron and clay) in excess of 100 years service.
A better option
Flexible pipes don’t just provide short-term, on-site benefits to construction companies tasked with laying the utilities, but also provide long-term benefits to the eventual owner of the utilities.
If you want to discuss which pipes would be best for your project, speak to the experts in the JDP Technical Team for free, straightforward advice.